1. Pouring Casting Processing
Metal processing methods are divided into two main categories: material removal processing and non-material removal processing.
Machining without material removal is processing that does not generate metal debris such as casting, welding, and pressing.
On the contrary, the material removal machining method is a machining method that generates metal scraps (Bavia) such as cutting and grinding machining.
At BENKAN VIETNAM, we do not limit any processing methods, depending on the requirements of the product, we use appropriate processing methods.
Pour casting is a production method that involves melting materials at high temperatures and pouring into molds, then cooling to solidify into the desired shape.
In BENKAN VIETNAM products, this technology is used for the Adapter part of JINOX.
|
|
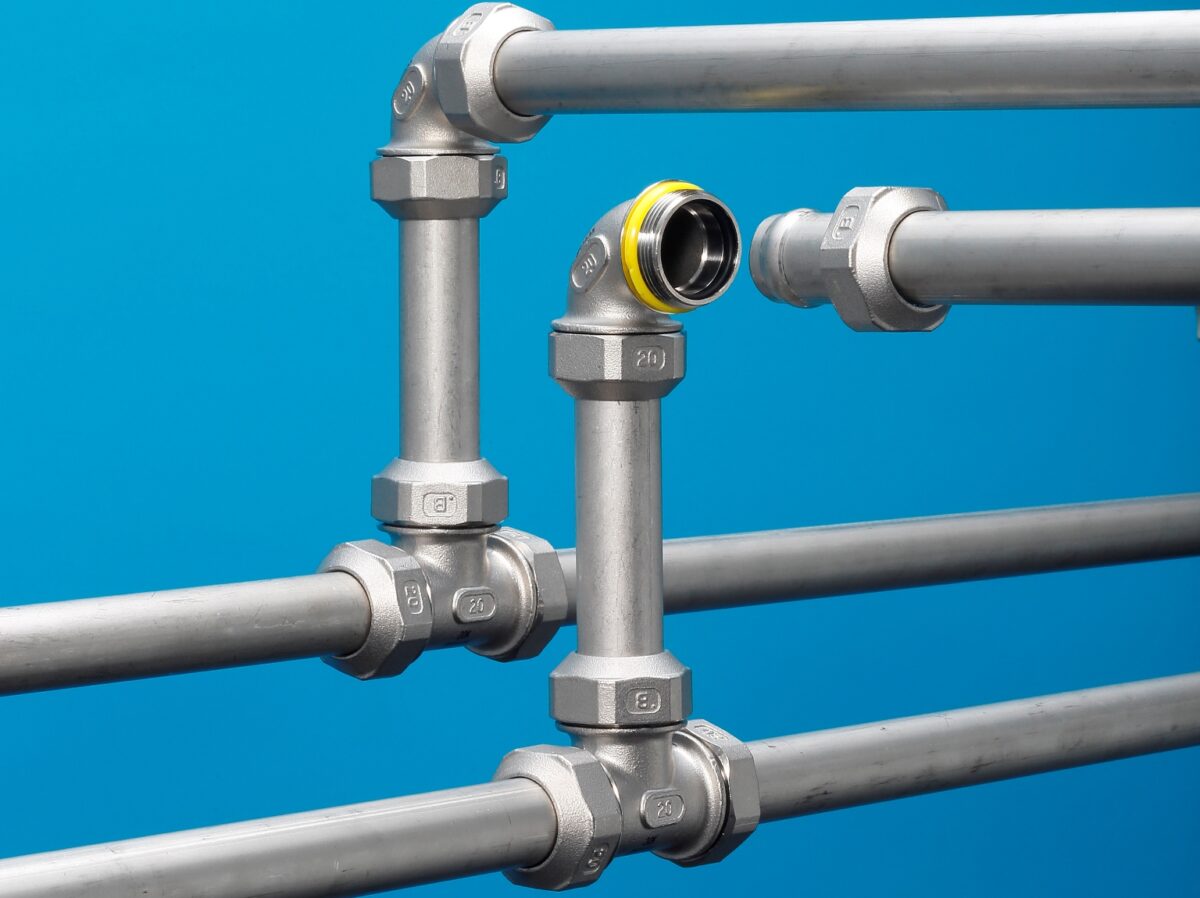 |
2. Lost-wax precision casting technology
In casting technology including sand mold casting, metal mold casting, and precision casting, “flow molding technology” is listed as one of the precision casting technologies, and it is being applied in Vietnam. BENKAN VIETNAM.
In "flow molding technology" there are also many types, and we are applying the thin shell mold method.
Casting on sand molds is a technology that represents most casting technologies. Sand molds are made by mixing silica sand - glue and hardener, then sealing them into wooden molds and heating them to fix them.
For flow molding technology, it has the following features.
・High dimensional accuracy
Compared with other casting methods, the deformation after casting is less, so the resulting product shape is almost the finished product, so post-molding processing steps can be reduced.
|
|
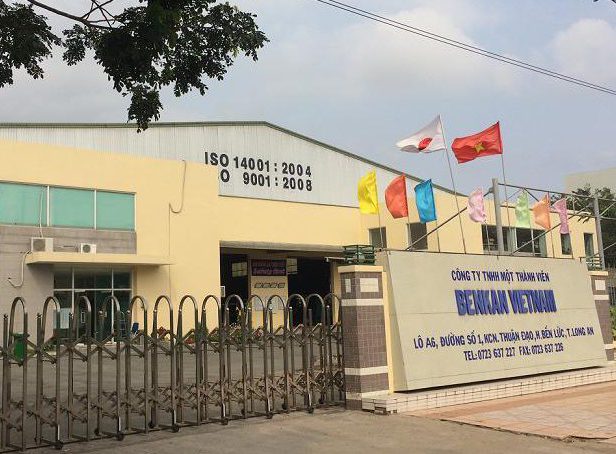 |
・The surface of the molded product is beautiful and sharp.
Products from flow molding have been used a lot, because of their ability to shape difficult products, including creating sharp letters or logos.
・Preferable for products with complex shapes
Capable of meeting large batch production of products with difficult profiles such as 3-dimensional curved surface shapes.
When using mold cores, to create space in the product, it also creates something special in the design that cannot be achieved with other methods.
And after connecting all the parts together, it will increase the level of responsiveness, so more production steps can be reduced.
・Choose from a variety of materials.
A wide variety of materials can be used such as carbon steel, special steel, stainless steel, tool steel, aluminum alloy, copper alloy. Can also be done with hard metal materials that cannot be machined or brittle alloys that cannot be forged or welded.
・Flexibility with large and small batch production
We are able to produce a wide range of products, from mass-produced products in lots of several thousand pieces to small-volume products of several dozen products. Currently, lost wax casting is used for aircraft parts, medical parts, etc., and precision casting is used in a wide range of industries.
|
|
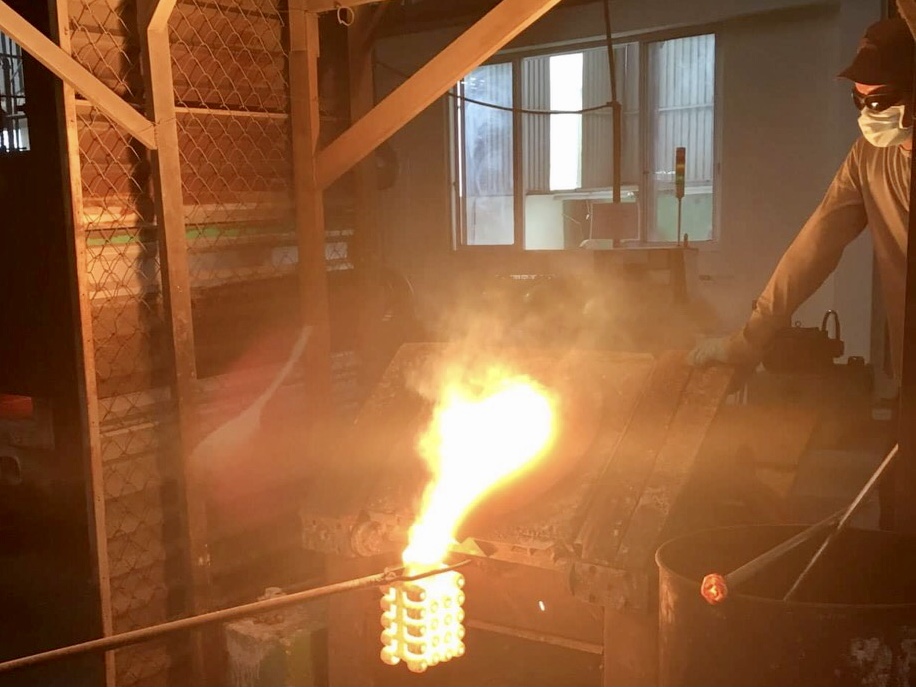 |
3. Overview of the production process
Overview of the process of "Flow Casting Technology", first it is necessary to create a wax model similar to the shape of the product, then cover the model with sand and quartz, and melt the inside to create A mold with a hollow core is a product model.
1. Wax injection
The wax is melted and shaped into a wax pattern similar to the desired product through pre-design and processing.
2. Wax pattern tree
Attach the shaped wax pattern to the tree branch.
The tree branch is used as a path for the molten material to travel to fill the product.
Because the shape after attaching the product resembles a "tree branch", it is assimilated like that.
3. Molding coating
The wax sample is coated with materials that are resistant to high temperatures and have little deformation such as sand, Zircon powder and Silica glue.
The coating dipping steps are repeated until the mold reaches the specified thickness and must be completely dried.
4. Dewaxing by heating
After the mold has been completely dried, it is placed in the oven to heat and apply pressure to remove all the wax from the sand mold.
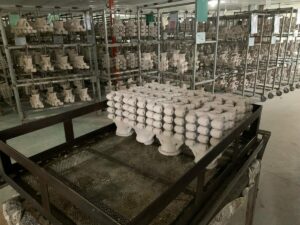
5. Burnout Kiln
For the purpose of strengthening the sand mold and at the same time completely removing the remaining wax in the mold after the waxing process, it is necessary to bake the mold at a temperature of 1,000~1,200oC.
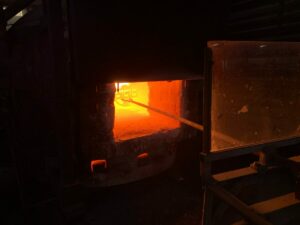
6. Casting
After the mold has cooled, use a hammer to remove the outer layer of sand.
7. Break the mold
After the mold has cooled after pouring, use a hammer to remove the sand layer on the outside.
8. Cut out and grind
The ridge attached to the top of the product will be cut off with a cutting stone, and the product will be obtained.
At this stage, when you discover unsightly parts on the product, use a belt sander to correct them.
9. Heat treatment
The heat treatment step is to return the material to its original mechanical properties of stainless steel.
Products cast using flow molding technology will be better than products cast on sand molds, because of better dimensional accuracy and surface smoothness.
Next, the positions that need cutting will be mechanically processed, threaded, inspected and packaged.